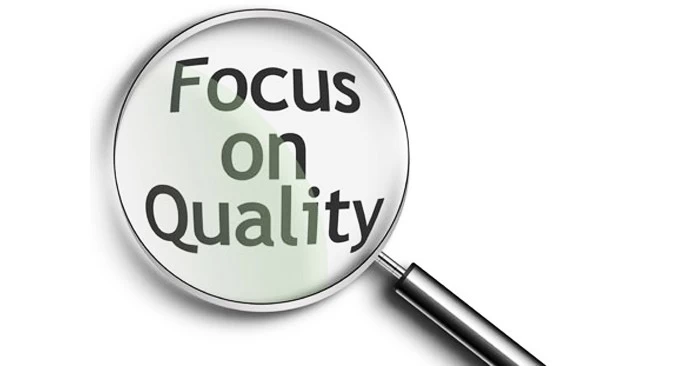
PRODUCTION & QUALITY ASSURANCE
For all the energy and passion that are invested in the development of a product, in the last resort the quality in series production must comply with the specifications from the development section. The following explains on the basis of the manufacturing process what it is that makes up the unique quality of AURORA helmets.
Production of the helmet shell
Aurora Sports exclusively uses fibre-reinforced plastics that offer the best properties for the manufacture of a helmet shell. Thanks to having many years of experience and highly specialised employees, Aurora Sports is in a position to produce helmet shells that are extremely strong and yet light. Each helmet shell is marked personally by the employee who is responsible for it and thus puts his name on the line for the quality of this example.
Laser cutting
Here the helmet is given its final shape. All the protrusions that area created in manufacture are cut off. The openings for the visor and ventilation are burnt into the helmet shell with a laser. Finally the helmet is checked to ensure that it has the correct material thickness and weight.
Painting
Even though many production steps have been automated today, it is not possible to dispense with hand work in some areas. Aurora Sports combines hand work and automation in production to ensure superlative quality. *You can find further details on the painting under the Hand work heading.
Final assembly
The ventilation sliders, visor seals, inner shell and padding are assembled with great care. The helmet only goes for sale after the subsequent detailed final inspection.
This strict compliance with the production processes with associated quality control guarantees the constantly high quality.
HAND WORK MAKES THE DIFFERENCE
1. The priming
After the helmet has been taken from the mould and all protruding parts and openings have been removed by a laser, the helmet is given its first priming. Then it is sanded and polished by hand and thus gets a flawless surface for the subsequent painting operations. Working on the various helmet shells with their own peculiarities requires a high degree of experience.
2. Checking the priming
After the priming the helmet is carefully checked for any small blemishes and passed for further painting – but only if the surface is absolutely perfect.
3. The painting
The quality of a painting operation depends on the quality of its individual layers. It is virtually impossible to apply a high-quality coat of paint by machine even with the very latest polyurethane paints. For that reason only specially qualified employees are used in this work step.
4. Checking the painting
Subsequently the paintwork is subjected to close inspection for drips, inclusions and unevenness.
5. Applying the design
Elaborate, extremely detailed and spectacular graphics are part of the brand image of a AURORA helmet. In a very complicated work step the designs are applied by hand by specially trained workers to the finished painted helmet.
6. Protective varnish
The last step in the painting process is the application of a clear varnish to the shell to protect the decoration and to give the helmet its unmistakable brilliance.
7. The final inspection
Before it is passed for final assembly, the finished paintwork of the helmet is given one last meticulous inspection. Perfection, even in areas that are hardly visible.